Our Services
Enterprise Transformation Engagements
Want to launch your own Continuous Improvement transformational journey. We can customize an end-to-end solution that will structure your journey based on Lean Six Sigma methodology. The engagement is structure around 5 elements: Customer, Leadership, Processes and Technology. We will become your in-house Transformational Agent utilizing a Learn, Do, and Teach plan. We will encompass the entire Value Stream, but will focus functionally to drive early success and build momentum. These engagements last between 12 weeks to 18 months depending on the size of the enterprise.
Workflow Analysis
Our Work Flow Analysis offering is a 5-day “baseline” evaluation of your targeted operation. During the assessment, we will evaluate Current State through a Lean prism. We will map the flow of your product and the efficiency of the “people”, and provide a written assessment for Areas of Opportunity as well as recommend Future State solutions. We can also help in the deployment of the identified improvement opportunities as part of our Kaizen Workshops offering.
Operational Excellence Assessment & Change Acceleration
In alignment with the Shingo Model, this area of service for our customers is focused on enterprises that have embraced and embarked on a Continuous Improvement (CI) journey. Our assessment will focus across four (4) elements: People, Process, Leadership and Technology. and vertically. We will focus on the depth and “operationalization” of CI Culture, alignment, tools, leadership & management. A report and scorecard with gaps and countermeasures is issued. Our firm is available to support and help deploy the countermeasures to accelerate the transformation.
Six Sigma Training & Expertise
The objective of the Six Sigma methodology is the implementation of a measurement-based strategy that focuses on process improvement and variation reduction through the application of Six Sigma methodologies. The Six Sigma DMAIC process (Define, Measure, Analyze, Improve, and Control) is an improvement system for existing processes while Six Sigma DMADV process (define, measure, analyze, design, verify) is an improvement system used to develop new processes or products. At InsightsPros, we can customize the Six Sigma program to meet your needs. We offer on-site training for Yellow, Green, or Black Belts.
Strategy Design & Deployment
The driver for how you deploy a successful strategy is driven by how you develop it. At InsightsPros, we rely on the Hoshin Kanri Planning process. It takes into account execution every step of the way, we provide you with a systematic method of strategic planning and managing progress toward achieving your strategic goals. Our Strategy design and deployment is based on the seven-step Hoshin Planning process in combination with The Hoshin Planning Matrix which aligns your strategic objectives with the specific resources and action plans needed to successfully implement and sustain a multiyear deployment.
Lean Leadership
Our Lean leadership program is aimed at those ready to commit to an Operational Excellence journey, have a commitment to their employees, and a commitment to the system and commitment to making changes towards improvement. Lean is all about eliminating waste through continuous improvement, and the most valuable resource a leader has available to understand where the waste is coming from is through the people that see it every day. Our program is based on the Toyota Production System (TPS) principles. We offer on-site seminars to cover one or many of the aspects of Lean Leadership. Whether you are looking to build a program or want a Value Stream Mapping session, we can help you in delivering those at your site.
Some Companies We Helped…
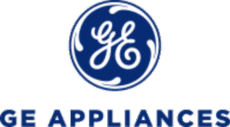
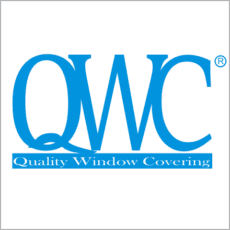
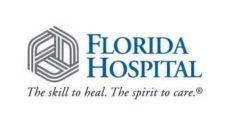
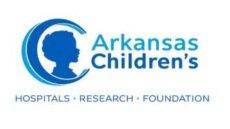

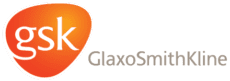
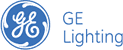
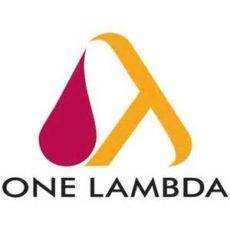
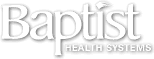
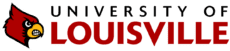
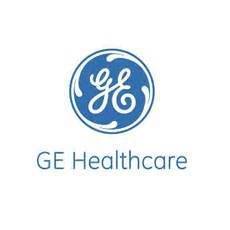
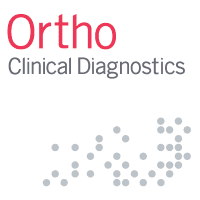
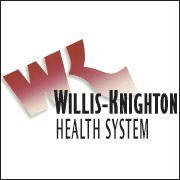
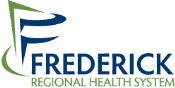
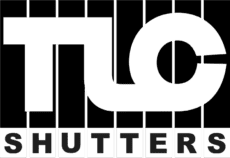
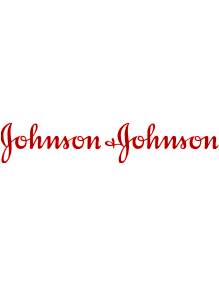
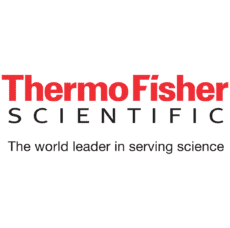
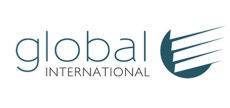
Contact Us